Twill carbon fiber fabric is a popular choice for composite projects due to its unique properties and aesthetics. It is made from high strength carbon fiber 1k , 3k, 6k and 12k. The twill and plain weave are the most popular weave patterns. They provide superior tensile strength in both 0/90 directions. The twill weave is more flexible and more glorious than the plain pattern, but it’s also easy to come apart and difficult to keep shape, so it should be handled carefully and spray some setting agent if necessary. These fabrics are not just good looking, but also with superior mechanical properties, like high strength, modulus, rigid, light weight, anti-corrosion, etc. For these properties, the carbon fiber fabric is desirable alternative to traditional materials, now the carbon fiber fabric is widely used in automotive, marine, boat building, racing, sports tools, even structural strengthening of concrete buildings.
The carbon fiber fabric can be processed in many ways, such as wet-layup, vacuum infusion. It can be wrapped on products to make it glorious and tough. We also supply carbon fiber prepreg, which is easier to handle than dry carbon fiber fabric, because it’s not easy to come apart and better resin control.
Features
- Signature aesthetics
- High strength to weight ratio
- High modulus for superior rigidity
- Anti-fatigue
- Increased Drapability: Compared to plain weave carbon fiber, twill weave offers more flexibility. This allows it to conform better to complex shapes and curved surfaces, making it ideal for intricate composite parts.
- Greater Strength-to-Weight Ratio: The diagonal weave pattern in twill fabric creates a longer fiber path compared to plain weave. This translates to a higher fiber volume and improved mechanical properties, offering more strength without adding significant weight.
- Enhanced Aesthetics: The diagonal twill pattern creates a visually appealing herringbone texture on the fabric surface. This is often desirable for applications where the final appearance of the composite part matters.
Twill carbon fiber fabric is used similarly to other carbon fiber fabrics in composite projects. Here’s a general process:
- Preparation: Choose the right twill weave fabric based on weight, tow size, and desired properties for your project. Prepare the mold or surface for layup by applying a mold release agent.
- Cut and Layup: Cut the fabric pieces to fit the mold shape, considering the drape and directional bias. Layer the fabric according to the design and resin system requirements.
- Resin Infusion: Apply the chosen resin system (e.g., epoxy) following the specific instructions to ensure proper saturation of the fabric.
- Consolidation and Curing: Remove any trapped air using consolidation techniques like vacuum bagging. Allow the resin to cure completely based on the specific resin system.
- Finishing: Once cured, remove the part from the mold and trim any excess material. Sand or machine the surface as needed for the final finish.
Packing
100meter per roll, the biggest width 150cm, one roll for each carton, then packed in pallet, wrapped with plastic film.
Transportation
For small order, we recommend shipment by DHL and FedEx. For bigger order, more than 4rolls, we recommend air freight. Because of carbon fiber is light weight, air freight is more preferable than sea shipment. We sell globally, please don’t hesitate to contact us for product and price details.
Project Showcase
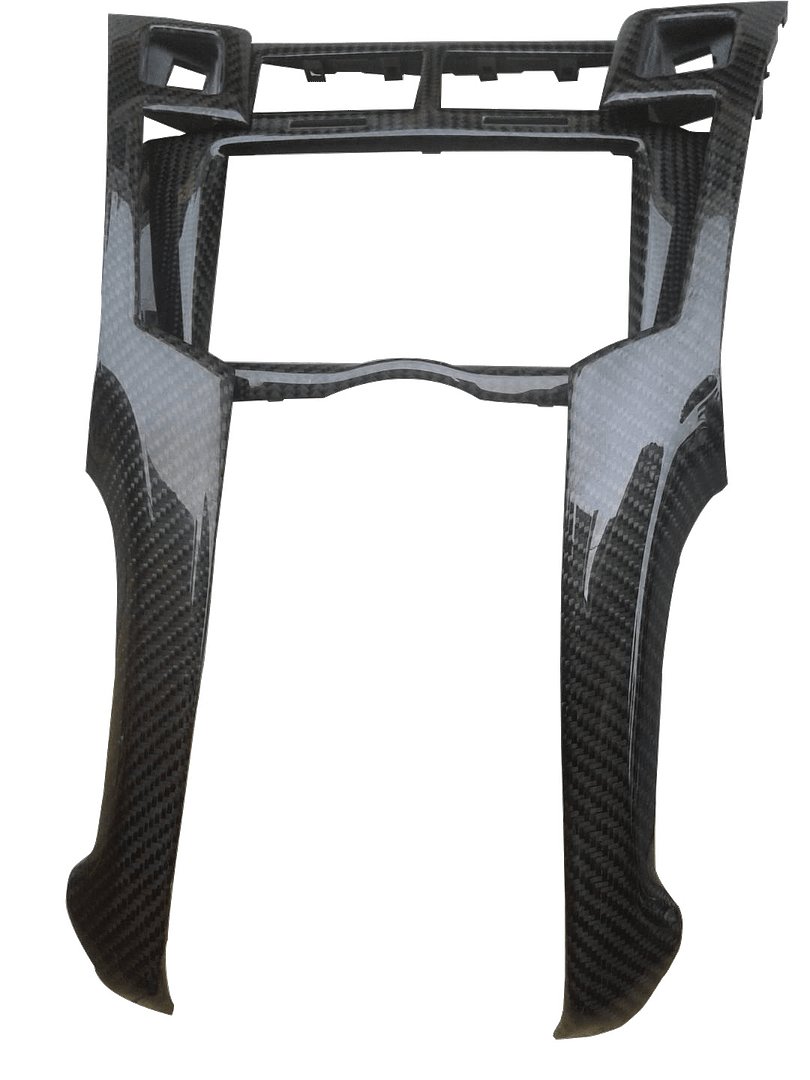
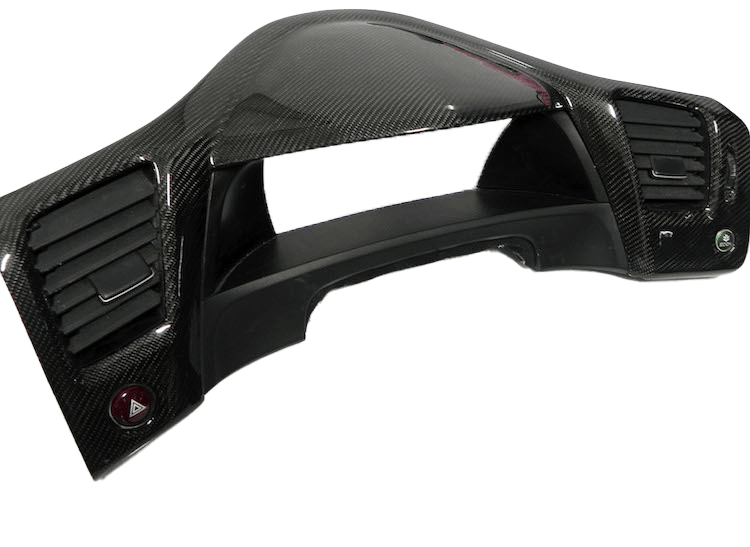